Climate change drives new focus on tank top protection
As Australia’s drought deepens and the UN warns of the worsening effects of climate change, local industries are moving to protect their water and process fluid tanks from heat stresses, high winds, evaporation, airborne pollution and wastage.
“Tanks now are being built to hold their contents more safely and securely than ever before, and protect it for longer and in more challenging operating environments,” says tank bearing engineer and manufacturer Mr David Booty, Manager, Hercules Engineering (a division of Cut To Size Plastics).
Steel, concrete and fibreglass water and industrial fluid tanks need secure roofs that can withstand expansion and contraction caused by factors such as increasing climatic and load variations, says Mr Booty, whose company is currently supplying bearings for roofs to protect tanks with surface areas as large as 10,000 sq m (100m x 100m, holding 90ML of water, the equivalent of dozens of Olympic pools).
He says such protection is needed for even larger tanks used by industry for applications as diverse as potable, process and firefighting water.
“They can hold upwards of 10, 20 or even 30,000 tons of liquid that must be protected from the elements and from pollution to safeguard it for use in water, wastewater, emergency fire protection and high purity industrial processing applications.”
A challenge facing developers and operators of buildings and processing plants for industrial and municipal uses is ensuring their top structures can flexibly cope with internal movement from climatically induced expansion, contraction and wind and rain forces. They also must cope with production stresses caused by heavy and changing loads, vibration and other factors encountered within diverse industries – as well as dust, bird droppings, rain-borne impurities and other airborne pollutants that can affect tanks used by industries in remote, rural and grimy urban settings, including industries such as agriculture and primary production, energy, oil and gas, ports and infrastructure, food and beverage, manufacturing, materials handling, water and waste water utility and emergency services.
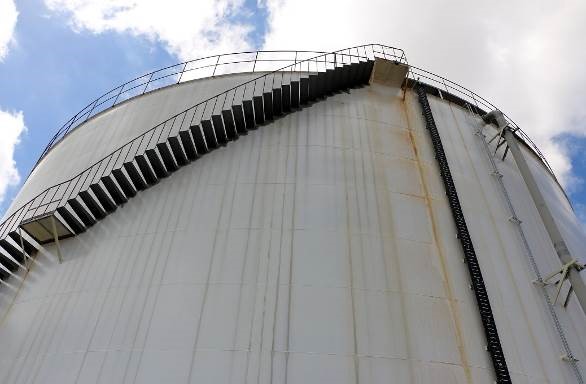
Herculon Type D Tank Top Bearings (HLD/TT) Bearings featuring stainless steel top, with Heruflon centre and Hercupad base
One cost-efficient solution to many such issues is offered by Hercules Engineering through its range of Herculon Type D Tank Top Bearings (HLD/TT) Bearings, which are custom designed for easy installation under roof beams of tank tops and other lighter structures, including some building roofs. These low-friction easy-slip bearings are particularly useful where loads are relatively small but both lateral and uplift forces need to be accommodated, says Mr Booty.
“Light but strong and flexible tank tops are now widely employed to protect tanks and their contents from external pollution. The bearings used under these tops must not only support the structure, but also prevent it from cracking and breaking and becoming part of the pollution problem.”
HLD/TT bearings are part of a proven range of Hercules composite slip joints and structural bearings for a wide variety of structures and weights incorporating engineered high-performance combinations of engineered thermoplastics and metal facing surfaces. Complementary Type D Herculon Bearings HLD/SG are designed to accept a lateral load of 30 per cent of the vertical rated load, which can be up to 600 kN per bearing in stock sizes, with higher capacity available custom-engineered for particular applications
HLD/TT bearings consist of a thin stainless steel slide plate with two stainless steel studs flash welded to the upper face. The lower face is highly polished, and the plate is provided with two slotted holes for uplift through-bolts. This plate slides against a Herculon- coated Hercupad, which has two clearance holes drilled into it. Characteristics include:
- Five stock sizes in working loads from 50-70 kN. Larger capacities and different dimensions can be custom engineered.
- Co-efficient of friction 0.05- 0.08, depending on stress
- Expansion capacity up to ± 20mm (can be custom designed for larger movements)
- Maximum rotation up to 0.01 radians
- Maximum temperature 80 deg C