CNC Design invests in Application Centre
CNC Design is investing more than $3.5m in the establishment of its new CNC Design Application Centre, which will feature Innomerix, within the new advanced additive manufacturing centre.
Founded in Melbourne in 1984, CNC Design has established itself in recent years as a pioneer in the design and manufacture of large-volume 3D printing and machining systems.
Situated in a facility close to its head office in Nunawading, eastern Melbourne, the new CNC Design Application Centre and the Innomerix facility will focus on two key areas: the development and testing of new advanced composite materials for additive manufacture; and the expanded development of CNC Design’s range of VSF thermoplastic, wax and concrete printers, including support for customer applications and training.
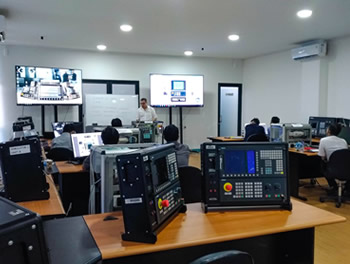
“We’re thrilled to be announcing our new Innomerix subsidiary, which will be co-located in our advanced application centre, situated here at CNC Design,” says Bruce Rowley, managing director and owner of CNC Design.
“This is one of the most exciting areas of development in additive manufacturing today, with potential applications ranging from the maritime and construction industries, to production of hydrogen fuel cells.
“The launch of both the CNC Design Application Centre and Innomerix builds on CNC Design’s work in this field to date and puts us at the forefront of innovation in this area going forward.”
Innomerix will be the first Australian manufacturer of high-performance thermoplastic composites, producing a range of thermoplastic compounds using different additives and reinforcement materials such as synthetic fibres like carbon, Kevlar and glass.
Taking its name from a combination of the words ‘innovation’ and ‘polymeric mix’, Innomerix will further advance the company’s innovative work in material technologies.
The facility will specialise in creating new materials for additive manufacturing, in particular aiming to reduce the cycle-time for the development of new composite materials for 3D printing, and thereby making the process more price-competitive compared with other manufacturing techniques.
One key area of focus for Innomerix will be in researching innovative methods for improving the environmental footprint of manufacturing, through the development of novel, sustainable high-performance materials using bio-based reinforcement fibres such as hemp, flax, bamboo, basalt and jute.
Nano-composites will be another priority, making customised materials that incorporate nano-scale additives like graphene, carbon nanotubes and clay.
At the heart of Innomerix will be a test laboratory for material testing and certification, equipped with a range of state-of-the-art additive manufacturing technology developed by CNC Design under its Virtual Smart Factory (VSF) concept.
These will include a VSF 211 large-area composite printer, and a CNC Design VSF Robot for eight-axis composite printing.
The VSF 211 printer is built around a double-bridge gantry for thermoplastic printing and five-axis milling, with a maximum volume of 12 metres by 5 metres by 1.6 metres.
The machine features a Siemens SINUMERIK ONE CNC system with DIGITAL TWIN; a VSF Model 60 composite print head capable of printing up to 150 kilograms per hour, with pellet drying and conveying; a 10kW, 20,00rpm HSD five-axis milling head; and a carbon fibre filament winding backstand and head.
The VSF Robot printer is based on a Comau six-axis robot coupled to a Güdel TMF floor-mounted track with indexing table. It also features a SINUMERIK ONE system with a Run MyRobot /Direct Control, and a VSF Model 19 composite print head.
The two systems can also be combined and controlled by a single SINUMERIK ONE CNC system with a total of 23 axes. Combining technologies for additive and subtractive manufacturing as well as filament winding, the system will be capable of large-area 3D printing, in five or six axes, of advanced thermoplastics with additives such as carbonfibre or graphene. Innomerix will be Australia’s first fully DIGITAL TWIN site.
The Innomerix centre will also feature the only compounding line of its kind in Australia, enabling the manufacture of composite materials in pellet form, with a production capacity of 250kg/hr. An automated packing line installed on-site will bag the pellets in 25kg bags.
“We are using cutting edge compounding technologies to make sure our materials meet the most stringent standards,” says Vahid Montazeri, Materials Engineer at CNC Design.
“With five high-quality precision feeders, we are capable of incorporating different additives with astonishing consistency. The increased operational flexibility provided by the extruder’s length/diameter ratio, coupled with state-of-the-art Siemens control systems, gives us a unique compounding capability in the region.”