“MOM’s” the word for manufacturers getting a competitive edge
By Rob Stummer, Asia Pacific CEO at SYSPRO
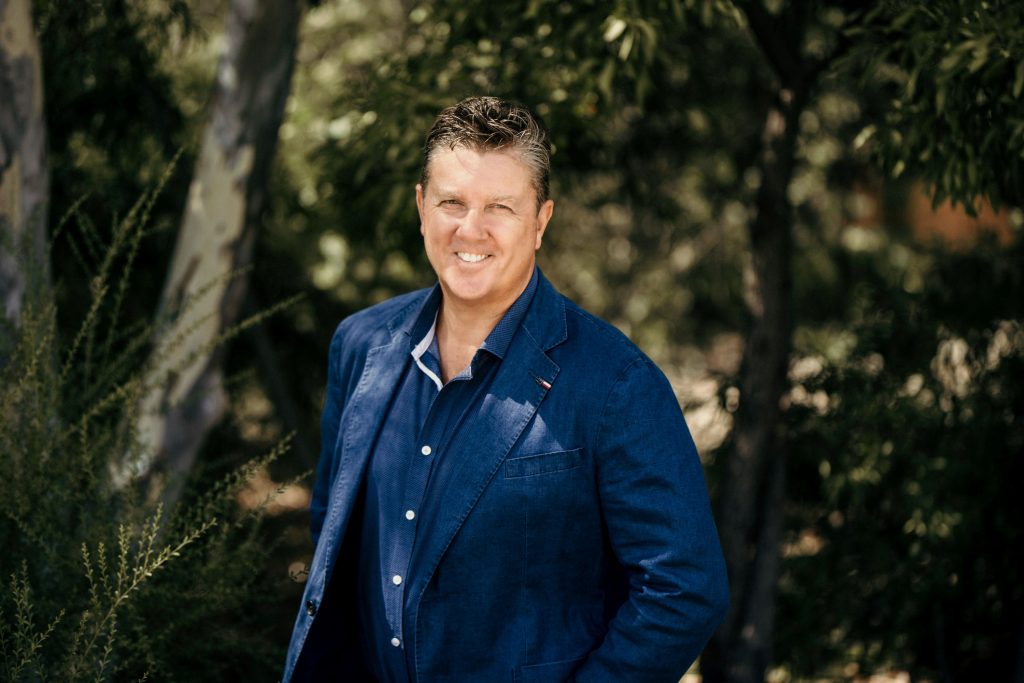
The manufacturing sector is incredible with how almost two years into a ‘new normal’, a pandemic is not letting the industry reduce the productions of goods that the world demands.
What has remained constant is the expectation that costs and waste stay minimal while the business functions efficiently.
Without a doubt, manufacturing is a globally competitive industry that’s often responding to market supply and demands.
The unpredictability of some market conditions can make it challenging for domestic manufacturers to often operate efficiently but there are solutions that can help business gain a competitive edge through better operational efficiencies.
Most factories have a myriad of data sources that are often neither connected nor integrated.
To harness the power of big data analytics and operational optimisation in manufacturing, it is critical to ensure interoperability between data sources.
The issue is that from a data collection perspective, every machine can in theory generate megabytes of data that is often not used to its full potential.
But what is the best way to improve operational efficiency in a manufacturing environment?
Manufacturers should fully embrace connected and automated manufacturing by digitally transforming their operational processes, because connecting with machines to read real-time data without manual inputs will drive efficiency and transparency to manage operational performance better.
The best way to achieve this is to ensure the intelligent interconnectivity between automation, digitisation and data analytics, which will drive transformative change within their operations and help them realise the promise of Industry 4.0.
The changes this industrial revolution promises are profound and over the next decade, forward-thinking manufacturers will transform themselves through digital interconnectivity.
Industry 4.0 is heralding a transformation in the manufacturing sector by facilitating new ways for humans and machines to work together and empowering manufacturers to achieve greater insights, reduce the risk of error and make better decisions.
It encompasses three technological trends driving this transformation: interconnectivity, intelligence and automation.
It converges IT (Information Technology) and OT (Operational Technology), to create a cyber-physical environment, which has been made possible due to the emergence of advanced Industry 4.0 technologies, including the Industrial Internet of Things (IIoT), big data, cloud computing, additive manufacturing, robotics and augmented and virtual reality.
These technologies combined are digitally transforming manufacturing through the integration of previously disparate systems and processes through interconnected computer systems across the value and supply chain.
Embracing Industry 4.0 opens a multitude of benefits for manufacturers, including improved agility, flexibility and better operational efficiency.
Connecting research, design, engineering and manufacturing enables manufacturers to reduce the time it takes to bring new products to market, resulting in faster responses to customer needs and better operational efficiency.
Translating real-time factory and supply chain data into insights enables manufacturers to respond a lot faster to changes in customer demand as well as market disruption, as has been seen in the past year during the pandemic.
By connecting operations and supply chain data through the cloud manufacturers can continuously optimise their factories and products in real time.
This means they can improve products throughout their lifecycle and this optimal level of agility through digital interconnectivity leads to higher sales.
Where does “MOM” fit in this picture? Manufacturing Operations Management (MOM) is the art of providing plant-wide manufacturing lifecycle management from planning, scheduling, publishing, collecting, tracking and analysing to optimise and improve end-to-end manufacturing operations.
The software element of MOM is called a Manufacturing Execution System (MES), which combined with an Enterprise Resource Planning (ERP) system, offers a unique level of delivery, cost and quality control of manufacturing operations for job shop, batch production, production line and mixed mode environments.
Manufacturers can also use a MES to measure performance to achieve world class standards of operation for overall equipment effectiveness (OEE) and total effective equipment performance (TEEP).
Also, a MOM allows manufacturers to optimise operational efficiencies through better workflow of core manufacturing activities, including schedule, publish, collect, track, analyse and improve.
Additional benefits of a MOM include increased productivity and lower costs by minimising loss within the business. Perhaps the most important aspect of a MOM is the ability to connect machines and other devices to digitise the factory and gain competitive advantage.
The next logical step for manufacturers is to invest in digital acceleration to create smart factories with Industry 4.0 technologies that will be better positioned to manage future disruptions, which will enable them to be more competitive against foreign companies in the post-pandemic world.
Implementing a MOM system will ensure effective execution of manufacturing operations to help improve efficiency.
Only by understanding and harnessing the technologies driving Industry 4.0 and understanding the value of interconnectedness, will manufacturers achieve the competitive edge they are seeking.