Schaeffler-supported UNSW Hyperloop engineers excel in SpaceX high-speed pod competition
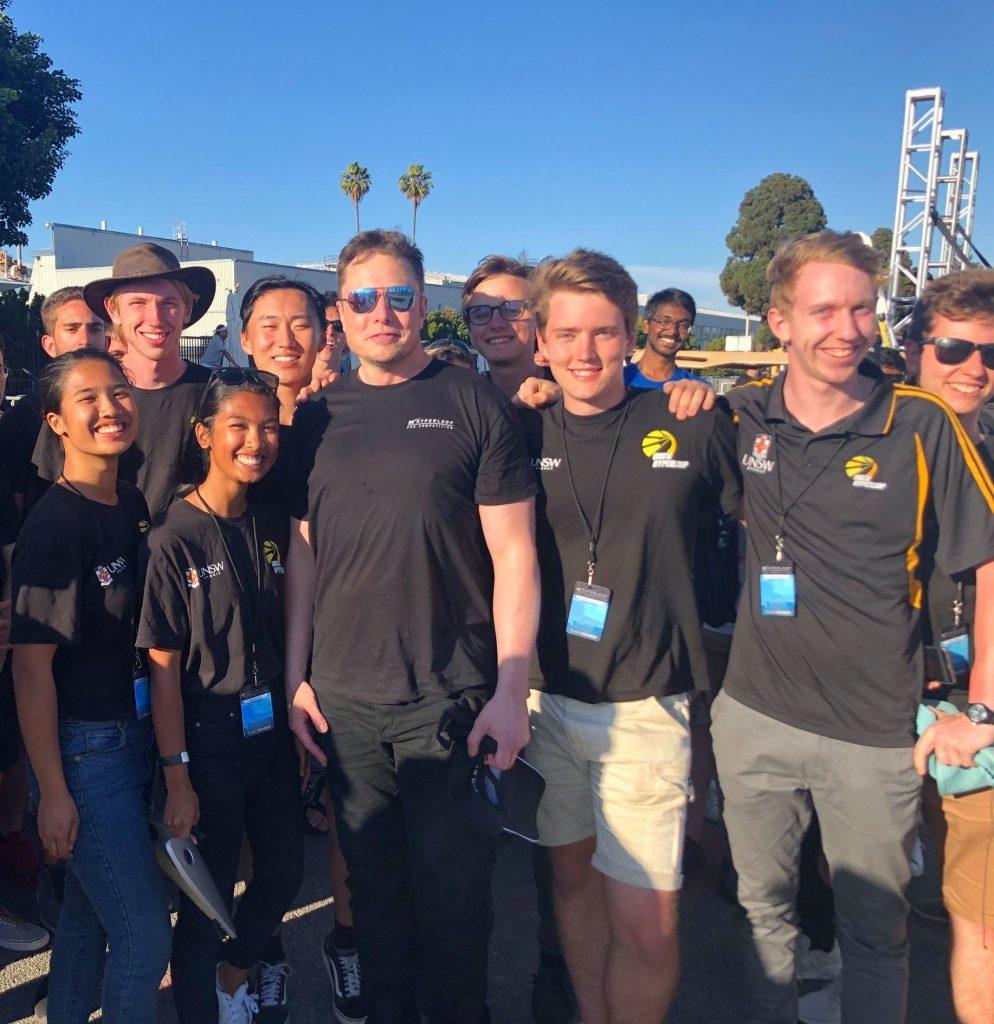
A competition highlight: UNSW undergraduate engineers – who recently competed in the SpaceX Hyperloop pod competition – got to meet technology entrepreneur, Elon Musk
Schaeffler Australia – part of the global digitalisation and Industry 4.0 leading Schaeffler Group – is taking a further step to enhance ‘mobility for tomorrow’ through its support of the UNSW Hyperloop engineering team.
UNSW Hyperloop – which comprises a team of undergraduate engineering students aspiring to innovate the future of high speed travel – recently competed in the SpaceX Hyperloop pod competition, where they placed 7th overall – the best result for a newcomer to the competition.
“As a company at the forefront of Industry 4.0 technologies, we are proud to partner with these bright young engineers, who have excelled in their first official Hyperloop pod competition,” said Mr Andre Kluge, Managing Director, Schaeffler Australia.
The SpaceX Hyperloop pod competition’s goal is “to support the development of functional prototypes and encourage innovation by challenging student teams to design and build the best high-speed pod.”
“In addition to placing 7th out of 21 teams, the UNSW Hyperloop team were the first ever team to successfully complete a self-propelled test run at a first appearance at competition level. However, I think the highlight for many students was getting to meet Elon Musk in person!” said Mr Kluge.
SpaceX Hyperloop 2019
The SpaceX Hyperloop 2019 competition was judged on the entrant’s pod’s maximum speed reached, with successful deceleration (i.e. without crashing). All pods were self-propelled and had to use their own communication system.
Previous winners of the competition have reached speeds of 284 mph (approx. 457 km/h) in SpaceX’s specially designed tunnel. 2019’s winner – Technical University of Munich – was also supported by Schaeffler, and managed to break that record and achieved 288 mph (463 km/h).
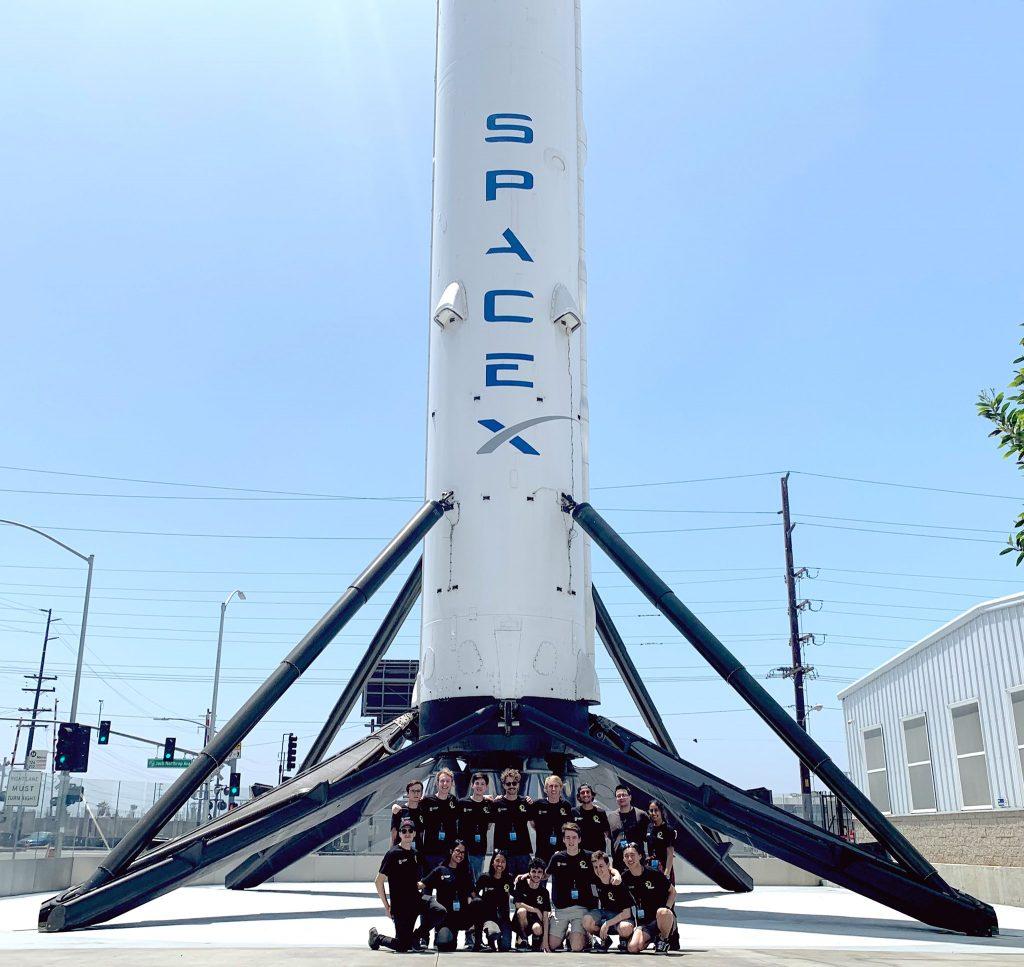
UNSW Hyperloop’s team visits SpaceX before competition day
Schaeffler’s digitalisation agenda
Schaeffler Australia collects more than 40 million characteristic data points annually through its diverse suite of digital technologies, including condition monitoring devices for mining and resources, pumps, fans and machinery and wind turbines.
“The support of the UNSW Hyperloop team perfectly matches Schaeffler’s digitalisation agenda locally. We’re constantly looking at ways to make industrial operations safer, more efficient, more productive and more cost-effective through the collection and analysis of important data,” said Mr Kluge.
“We decided to collaborate with UNSW Hyperloop because it’s important to support the future engineers of this country. Schaeffler places a high importance on education and pushing the boundaries of engineering excellence.”
Wind 4.0 – how Schaeffler’s digital technologies are shaping the wind industry
One of the industries where Schaeffler Australia is already shaping the future through digital technologies is in wind power generation. Its condition monitoring technologies are used to collect data on core components of wind turbines and avoid costly downtime and maintenance by identifying when a component will need to be serviced or replaced.
Condition monitoring technologies – one of the core components of industry 4.0 – are a long-term investment. Wind farms typically have a 20-25 year life, and real-time condition monitoring of every bearing can provide valuable data and improve maintenance programmes throughout that lifespan. However, an up-front cost can often be a deterrent to the investment, especially when budgets are tight.
But it’s worth considering the costs throughout the entire life of a wind farm, particularly as the fleet ages, explains Mr Kluge.
Australian wind farms have typically anywhere between 10 and 200 turbines. For the purposes of this example, the figure of 10 turbines will be used. To place condition monitoring technology on the bearings of all 10 turbines could cost between $100,000 and $150,000, depending on the technology employed.
If no condition monitoring is in place, and a single main rotor bearing fails, the cost of repair or replacement, including tools, cranage and lost production time could cost between $350,000 and $400,000.
These figures show that if condition monitoring technology prevents a single failure, and saves on these costs, it has already paid for the cost of condition monitoring technology for an entire wind farm. In most cases, it would save these costs multiple times over throughout the life of the turbine.
Schaeffler Australia already has more than 120 online condition monitoring systems installed in wind farms across Australia. These systems collect approximately 138,000 characteristic data points daily, which adds up to more than 40 million per annum.