IIoT edge devices and gateways vital to a monitoring strategy
-Daniel Sultana, Country Manager, Australia and New Zealand at Paessler.
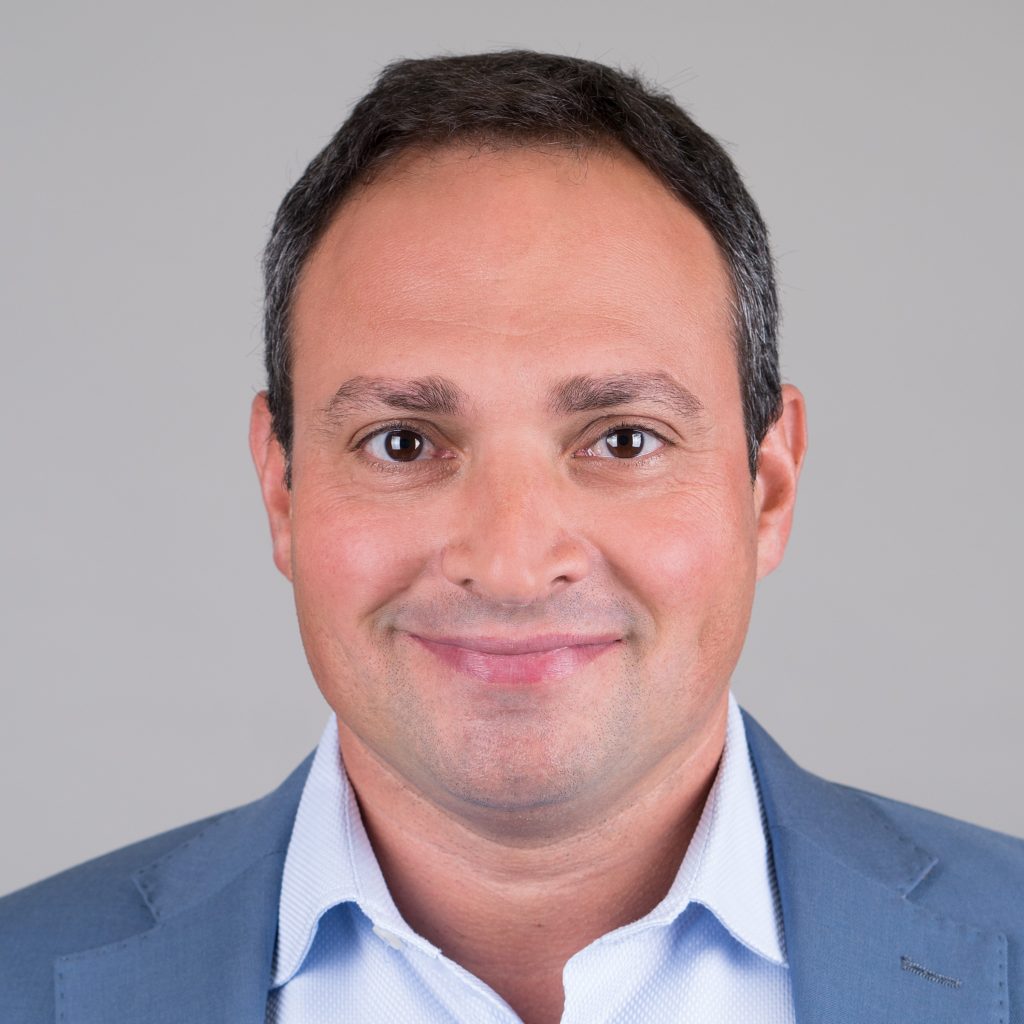
One of the key benefits of converging IT (Information Technology), OT (Operational Technology) and IIoT (Industrial Internet of Things) systems in a manufacturing business is that it enables a more holistic approach to manage the entire infrastructure.
The resulting digital interconnectedness provides vast improvements for manufacturers in terms of efficiency, reliability and profitability, but there are risks associated with IT/OT convergence, according to the Australian Cyber Security Centre.
What are IIoT gateways?
Industrial Internet of Things (IIoT) refers to a network of connected devices in the industrial sector and is a subset of the Internet of Things (IoT).
An IIoT gateway is a bridge between a field network and the IoT platform or sometimes a business application. IIoT gateways can be viewed as data aggregation points for field devices or wireless networks.
They provide local storage and compute capabilities as well as a user interface for data processing and system management.
The defining characteristic of connected devices on IIoT networks is that they transfer data without human-to-human or human-to-computer interaction.
Connected devices communicate through IIoT gateways, which are physical servers that filter data and transmit it to other devices and software applications.
IIoT gateways have therefore become a key part of a solution to monitor an entire infrastructure holistically, which provides a multitude of benefits for manufacturers that adopt it.
Since digital transformation in manufacturing started, more and more connected and smart devices are appearing in factory settings.
This includes sensors for monitoring environmental factors like temperature, humidity and vibrations, as well as devices needed for smart automation.
Building monitoring systems
There are concerning stories about poorly secured building automation networks being hijacked, resulting in hundreds of employees being unnecessarily evacuated and a loss of productivity.
For this reason, facilities management has become a new area that has adopted the use of sensors to help manage aspects like power consumption and even airflow around production, warehouse and distribution facilities.
Being able to monitor these environmental metrics as part of an overall monitoring strategy, gives a clearer picture of the entire environment.
For example, rising temperatures could indicate a problem with the Heating Ventilating and Airconditioning (HVAC) system and any spikes in temperature or humidity could pose a risk to certain machinery.
Knowing these values helps businesses make
decisions about other aspects of their infrastructure and will often facilitate
proactive steps to be taken to mitigate risk, even before a failure occurs.
The rise of the industrial edge
Many industrial automation vendors are drawing inspiration from information technology to address any challenges, turning to an approach known as edge computing, which is a form of distributed computing that moves computing resources closer to high-demand areas on the network’s edge.
With more resources at the edge, data can be prepared locally before wide distribution; modern security measures can be layered onto legacy systems and advanced functionality can be embedded in processes to support a resilient network.
Data is key to managing production processes effectively and needs to be gathered, analysed and utilised at all levels, from the production floor and throughout the entire facility right through to despatch.
This means that devices that were previously isolated, including programmable logic controllers (PLCs), industrial PCs and Remote Terminal Units (RTUs), now need to use different messaging protocols to connect to the cloud and other data collection systems.
Industrial MQTT
MQTT (MQ Telemetry Transport) is the most popular IoT-specific messaging protocol. However, there are various challenges with using MQTT in an industrial environment.
MQTT’s intuitive flexibility requires stronger guarantees of interoperability and state management to meet the needs of a diverse industrial network.
Furthermore, whilst MQTT provides a framework for large-scale integration and addresses essential cybersecurity concerns, MQTT on its own cannot create a secure IIoT infrastructure.
Implementing a scalable monitoring system
All of this has resulted in industrial edge devices becoming data aggregation points that are connected to various systems and therefore form a key part of a solution to monitor the entire infrastructure holistically.
In order to deliver a scalable monitoring system without worrying about vendor lock-in or IT infrastructure investments, manufacturers need to simplify the traditional architectures required to connect field assets to software systems.
The use of IIoT edge devices makes many applications more affordable and practical in the industrial setting.
The economic pressures and increased pace of technology adoption and digital transformation will continue even as the world recovers from the ongoing impact of the pandemic.
It is therefore looking extremely likely that system integrators, developers, engineers and technology consultants will look more frequently to IIoT edge computing in search of the kind of competitive advantage it provides.