Improving rail access at the Port of Melbourne
As part of their 2050 Port Development Strategy to define critical infrastructure needs and support the economic growth of Victoria, the Port of Melbourne initiated the Port Rail Transformation Project (PRTP) to improve rail freight access across the Australian state.
Spanning more than 500 hectares of land at the mouth of the Yarra River, the Port of Melbourne handles about a third of Australia’s container trade. The AUD 125 million railway initiative aims to facilitate and increase rail-road share. It will enable more containers to be moved by rail more efficiently by increasing rail terminal capacity and improving rail terminal operations at the port.
When complete, PRTP will provide a rail solution to meet the needs of a growing port and reduce truck movements across Victoria, particularly in Melbourne’s inner western suburbs. “It’s about taking more trucks off inner-city roads and putting more containers on trains destined for outer-suburban logistics terminals,” said Matthew Brooks, senior project manager of port rail infrastructure at Port of Melbourne.
With more than 130 years of technical excellence in transport infrastructure, WSP was selected as part of an alliance with the contractor and client to provide design consultancy services for the project. The scope of their responsibilities included designing and building a new rail terminal interfacing with one of the container terminals, as well as upgrading existing lines and connections to improve access and provide operational flexibility for all trains accessing the port.
To optimise design and efficiently meet the Australian community’s needs for mobility, connectivity, sustainability, and resilience, WSP set out to digitalise workflows and information management across the three organisations working on the PRTP.
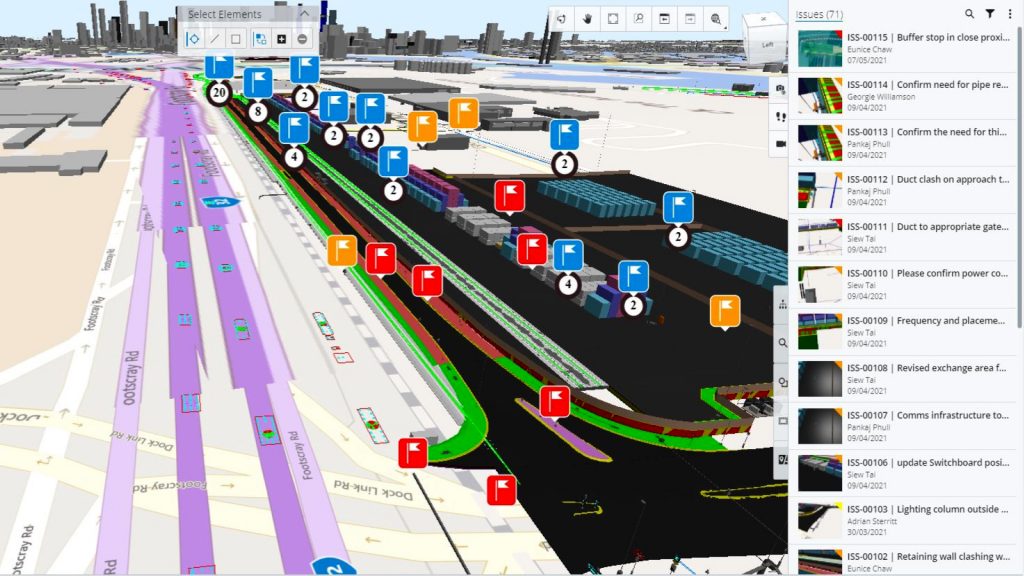
A Need for a Connected Digital Environment
With approximately 250 multidisciplinary project team members spread across three organisations, the project presented information management and coordination challenges, compounded by a tight submission timeline for preliminary and final designs.
“The final design planning stage was required to be completed in 12 weeks, including a preliminary design submission at the six-week mark,” stated Alexander Yamas, digital engineering lead at WSP.
Given the limited time between key milestones to produce a functional design, effective information management and collaboration were pivotal to successful and timely delivery. WSP needed to streamline workflows and ensure that the entire team had real-time access to all project models and data.
In the past, WSP’s project information was scattered across different desktop applications. “Typically for a multidiscipline project such as this, we would have inadvertently adopted tools that did not integrate with each other,” said Yamas.
The use of these multiple design platforms created incompatibility, IT security, and licensing issues, limiting access to key stakeholders and project staff and resulting in team members reverting to paper-based workflows.
Therefore, WSP would have to spend a significant amount of time installing additional software and manually managing the exchange and transfer of information. Committed to continuous digital transformation, WSP sought to improve not only the way that they manage information, but also their collaboration strategy to better connect all key stakeholders throughout the design phase.
They realised that, to timely meet the project deliverables, they needed to establish a connected digital environment that streamlines design coordination and provides greater access to information.
Leveraging Bentley’s Web-based Applications
Already familiar with Bentley, WSP selected their applications to create a cloud-based platform, providing a single source of truth for all users to publish, access, visualise, and share key project information in real time. Leveraging ProjectWise and the Bentley iTwin platform, they established an integrated digital environment, streamlining workflows and automating the federation of 3D models and design information to enable virtual design reviews and issues resolution, as well as optimise deliverables management.
“Bentley’s cloud-hosted ProjectWise 365 integrated with iTwin Services provided a ‘one-stop-shop’ for information management for the entire project and a connected data environment that aligned with international standards and specifications,” said Yamas. The iModel Manager feature facilitated coordinated digital design reviews, where information and models were automatically synchronised between ProjectWise to iTwin, creating an iModel from any file format that was shared.
The team could capture any changes from ProjectWise that were shared or published within the iModel, ensuring that the content used by the stakeholders during the design reviews was always controlled and current.
General communication was another key aspect of the project where Bentley applications and a connected data environment were critical to meeting project milestones, including requests for information (RFI), transmittals, and issue tracking.
“An example of where Bentley technology became a true connected data environment was the ability to link into our project portal via web-based links to the RFI tools, transmittals, and even the issue resolutions, tracking all of our issues throughout the project,” said Robert Freeman, digital operations lead at WSP.
Transmittal issues were loaded into an interactive dashboard and digitally assigned with automatic status updates, facilitating real-time web-based issue comment, resolution, and close out. The integrated digital solution allows for real-time model sharing and data responses to be automatically tracked and visualised, optimising collaboration, issues resolution, and deliverables management among all project stakeholders.
Transforming Digital Project Delivery
Bentley’s integrated cloud-based technology solution provided controlled information and data sharing among design disciplines and stakeholders on the PTRP. Using ProjectWise, WSP collaborated live, facilitating coordinated, multidiscipline 3D design.
Integrating iTwin to share their design models with stakeholders on a weekly basis enabled digital, visual design reviews and a right-first-time design approach, resolving issues much earlier in the design process compared to conventional methods, reducing waste and rework.
“The reduction in rework helps make sure we meet deadlines and reduces the burden on the design team, particularly given the short time frame for delivery and the risks associated with that,” said Yamas. Working in the connected data environment streamlined workflows and stakeholder communications and automated 3D model coordination, resolving 3,200 issues throughout the preliminary and final design phase, saving 475 hours, and realising a total return on investment of 67.31%, or AUD 43,500.
As their first project using cloud-based applications to share and manage information across the entire design team and with the contractor and client, WSP challenged everyone to work collaboratively, bringing clarity and vision to the complex challenges faced on PRTP.
Bentley’s integrated web-based technology provided an open-source platform with extractable data, creating a single source of truth that was easily accessible, driving collaborative digital workflows and information management, transforming digital project delivery for WSP and within the industry.
“[The] Bentley iTwin [platform] provided a connected data environment to visualise, track, maintain, share, and analyse design information with all project stakeholders to reduce rework and add value.” — Robert Freeman, Digital Operations Lead, WSP