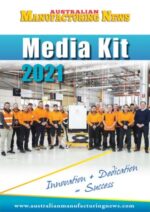
March 2021
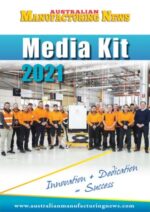
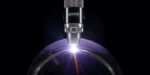
Aussie hi-tech welder to join global defence industry
A manufacturer of hi-tech welding equipment is embarking on a joint project with a huge global player that it hopes will help it gain a foothold in the lucrative defence manufacturing sector. K-TIG Limited, based in Adelaide, South Australia, has commercialised Australian CSIRO technology to weld materials faster and stronger than traditional techniques. Until now, the publicly-listed company has focused on the pipe, tank and pressure vessel industries. But this week, K-TIG signed a Memorandum of Understanding with major Korean company Hanwha Defence Group and Hanwha Defence Australia, to develop advanced keyhole welding procedures for armoured applications. Hanwha is South Korea’s largest defence company and also operates in aerospace, fintech, mining and clean energy. It is also the preferred supplier for the Australian Army’s Land 8116 self-propelled artillery project and shortlisted for the Land400 Phase 3 Infantry Fighting Vehicle project. The K-TIG system can perform a traditional six-hour weld in less than four minutes to a quality standard and, unlike traditional welding, it requires no edged preparation or filler materials. K-TIG managing director Adrian Smith said the MOU with Hanwha would trigger a 24-week joint project to demonstrate the K-TIG technology in Adelaide on the specific defence materials at specific joint geometries to prove its “superior hardness characteristics”. “Traditionally when you weld two pieces of armour together you change the mechanical properties because you melt the metal and recrystallise it around the joint and the joint is not as hard as the base metal,” he said. “But our technology and the way we weld in a single pass involves much less degradation in the strength of the joint so our joint hardness is comparable to the base metals plus we have less defects. A Hanwha k9 self-propelled howitzer. Picture: Hanwha Defence. “Once we’ve proven the suitability then we will look […]
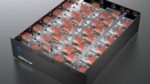
Energy Renaissance to deliver defence-grade cybersecure battery management system with CSIRO and IMCRC
Energy Renaissance, an Australian lithium-ion battery manufacturer, will develop a defence-grade cybersecure Battery Management System (BMS) for its superStorage family of batteries that are to be manufactured in Tomago, NSW. The A$1.46 million BMS project is jointly funded and developed by Energy Renaissance with Australia’s national science agency, CSIRO and the Innovative Manufacturing CRC (IMCRC). The BMS will monitor and report on the battery’s usage, lifespan and faults through a mobile network to Energy Renaissance and their customers. Communicating through an inverter, the system will enable secure real time data, analytics and remote management to drive down the risk of battery failure and operating costs for grid-scale energy storage users. Brian Craighead, Technology and Development Director of Energy Renaissance said, “The collaboration between Energy Renaissance, CSIRO, and IMCRC will promote an Australian Battery Management System instead of relying on an overseas technology platform. Working together with CSIRO will ensure we can create a world-class defence-grade cybersecure Battery Management System that is fully developed and managed in Australia for critical energy storage infrastructures.” “Software designed and developed in Australia has a strong global reputation and we’ve built a history and track record as an industry. Through this project, we will demonstrate the advantage that Australian intellectual property can bring to a highly competitive energy storage market where a superior Battery Management System is critical for the operating efficiency of a battery.” Dr Adam Best, Principal Research Scientist at CSIRO said, “CSIRO is delighted to be working with Energy Renaissance to develop a Battery Management System that is the ‘nerve centre’ of a battery, and will make batteries safer, more affordable and optimised to operate in high temperature environments. Our partnership with Energy Renaissance validates CSIRO’s capabilities to collaborate, train and transfer skills for the advanced manufacturing of batteries.” David Chuter, CEO […]
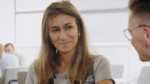
Fleet Space Technologies applies for a Federal MMI grant to build 50 nanosatellites a year
Adelaide satellite manufacturer Fleet Space Technologies has applied for a $5 Million Federal government Modern Manufacturing Initiative (MMI) grant so that it can jump from building three hand-built nanosatellites a year to mass-producing 50. Additional support from the South Australian government will supplement nearly $4 Million the company is raising itself. If the grant application is successful, Fleet Space will become a major satellite manufacturing hub and increase its payroll from 31 staff today to 128 by 2024, says its CEO and co-founder Ms Flavia Tata Nardini. Most of the new employees will be engineers and specialist satellite assembly technicians. Fleet Space has spent $12 Million since 2015 on R&D to develop the world’s most advanced beam-steering antenna and to miniaturise its satellites’ communications payload. These make it possible to deliver its Nebula space-based data network using a 10kg nanosatellite where previously this level of connectivity was only possible with a 100kg satellite. The company, which has already launched four nanosatellites, has applied for a $5 million grant under the Department of Industry, Science, Energy and Resources’ Modern Manufacturing Initiative (MMI) to help it make the jump. Fleet Space plans to build a new factory with more than double the space for R&D and manufacturing and has partnered with the University of Adelaide’s Institute of Photonics and Advanced Sensing, local company Redarc Electronics, Hawker Richardson in Melbourne and NSW-based Lintek to build the industrial capability to manufacture these nanosatellites in Australia. The Nebula service for utilities, mining and energy companies uses satellites to connect sensors monitoring critical infrastructure such as remote mine sites, alternative energy sites, gas pipelines and rurally dispersed electricity pylons with central base stations, 24 hours a day. This also allows operators to conduct geological surveys and operate unmanned vehicles such as drones remotely from a proper […]
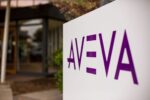
AVEVA and OSIsoft combine to unlock potential for industrial organisations
Industrial Software Market Leaders Introduce ‘Performance Intelligence’ to create Industrial Software and Data Leadership AVEVA, a global leader in engineering and industrial software, has joined forces with OSIsoft to meet the expanding information management needs of industrial companies and accelerate their digital transformation. The combined portfolio brings OSIsoft’s world-class data management together with AVEVA’s leading industrial software to unlock Performance Intelligence. Providing greater operational agility and resilience, Performance Intelligence connects information and artificial intelligence (AI) with human insight, to enable faster and more accurate decision making, helping industries boost sustainability. By pairing the trusted capabilities of OSIsoft’s PI System with the leading industrial software of AVEVA, Performance Intelligence gives the people behind essential processes the rich, reliable data they need to better measure and understand the entire industrial lifecycle. Areas where Performance Intelligence is likely to have the most impact will include organisational productivity, operational agility, and sustainability. The global big data and analytics market is growing exponentially and projected to be worth $274 billion by 2022. Staying ahead of the curve requires a new understanding of the scope and scale of industrial information to leverage that data effectively. Insight into industrial information from edge to enterprise reduces downtime, production costs, and energy consumption – optimising resources and driving sustainability. The combined software portfolio is driving digital transformation for over 20,000 customers globally, operational efficiency to empower people, industries, and communities. Craig Hayman, CEO at AVEVA, said, “Together we’re redefining the capabilities of industrial software. Through Performance Intelligence, we can see worlds of data from bold new angles, and inspire better understanding of complex value chains, to boost performance and drive sustainability. The combined impact of AVEVA and OSIsoft will enable our customers to manage complex industries more efficiently. Our expanded capabilities elevate AVEVA’s commitment to deliver operational agility that […]
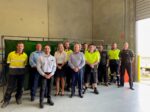
Hydraulink “can do” Dandenong branch rewarded for hard work during tough Covid conditions
The hardworking attitude and “can do” ethos of the Hydraulink Dandenong branch has earned the accolades of Managing Director Denis Matulin, for the staff’s dedication during challenging Covid conditions. The extended Covid lockdowns posed major challenges for this Victorian branch, as it did for many businesses across the state. But Hydraulink Sales and Service Technicians (HSSTs), along with branch staff, rose to the challenge, and worked within strict hygiene rules to provide breakdown services and other hydraulic work required by busy industries seeking maximum uptime. “Hydraulics are vital to all hard working machinery, and businesses in industries such as forestry, agriculture, construction, civil engineering, materials handling and food and beverage needed our help more than ever,” said Mr Matulin. “It was harder to travel, harder to sign in to individual sites, and there were a lot more rules, but I’m incredibly proud that our whole team rose to the task and remained open throughout the entire pandemic, providing vital service to industry,” he said. The Hydraulink Dandenong branch is part of a network of more than 400 hydraulic service points across Australia, New Zealand and the Pacific Islands. The network operates under the market signature “best under pressure” and delivers essential, safety-compliant and traceable hydraulic hose, fittings and services with expertise to industries requiring prompt, quality 24/7 service – either on-site or off-site. Service Awards In addition to praise for the branch’s outstanding performance in the past year, Mr Matulin also awarded long-service awards to two staff members. Craig Dorling received his 10 year service award and Aaron Harris received an award for five years of service to the company. “As a company, we seek to form long term partnerships. That applies to customers, suppliers and employees. I’m delighted that these two talented employees continue to provide value to the […]
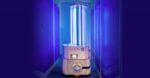
Disinfecting robot prepares for return of students
Gen2 is using the innovative technology to disinfect the workshop area and main atrium at its HQ and training centre in Cumbria, UK, ahead of welcoming staff and students back to the building. The remotely-operated robot was developed by Forth in Cumbria last year as a response to the fight against Covid-19. The firm is known for its innovations to solve complex industry challenges all over the world in nuclear, oil and gas, renewables and other sectors. Disinfecting of the workshop area and main atrium will enhance current Covid-19 safety measures in place throughout the building, and provide extra peace of mind for staff and students. Gen2 has worked closely with Forth over a number of years delivering apprenticeship programmes and training for the engineering firm, which is based in Maryport, Cleator Moor and Barrow in Cumbria. The Forth team developed the disinfecting robot in a matter of weeks by combining its tracked robot, vapour cannon, camera and lights. The robot is able to be worked remotely, controlled from a safe distance, to disinfect any area – inside or outside – to help the country safely emerge from lockdown. It can be used in offices, warehouses, transport hubs, schools, shopping complexes, or on the streets, anywhere inside or outside, wherever it’s required. It can be deployed in any building or any area, before people return after lockdown to make sure the space they are going back to is safe to use, and can be regularly re-used to decontaminate areas, whether that’s once a week or several times a day. Radio-controlled, wireless and tetherless, the disinfecting robot can perform fogging or misting. It has the ability to climb flights of stairs and can disinfect large areas in a matter of minutes. It works in a similar way to a vapour cigarette […]
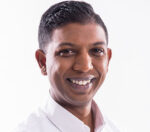
Futureproofing your manufacturing business to mitigate risk
By Kevin Dherman, Chief Innovation Officer at SYSPRO In 2020, Industry 4.0 technologies played a decisive role in many manufacturers’ pandemic responses and it helped these companies to keep their operations running during the crisis. Many were able to keep operating in the face of shortages of workers or raw materials, whilst others struggled to keep up with the sudden spike in demand. How did Industry 4.0 technologies help those companies in their efforts to reduce the negative impacts of the crisis and reduce the risks for their business? The SYSPRO 2020 Manufacturing CFO 4.0 Survey, which was conducted in October 2020, shows how manufacturers and distributors handled the operational shifts brought on by Covid-19. It revealed that 60% of manufacturers and distributors were impacted by supply chain disruptions. 47% of businesses were unable to function due to operational staff reliance on-site; while 29% of businesses felt that their business systems did not provide them with the availability and accessibility to manage the changes that the pandemic introduced. As these businesses attempt to stabilise, many are considering adopting emerging technologies and Industry 4.0 to mitigate the risk of major disruptions in the future. The challenge for many of these businesses is understanding which technologies to adopt, when to pursue this transformation and how to budget for it. There are several Industry 4.0 technologies that have real potential to help futureproof Australian manufacturing and distribution businesses in the next five years. The automated warehouse It is important to note that transitioning to an automated warehouse is a long and expensive journey. In most cases, it will take three to five years for manufacturing and distribution businesses to be fully automated. At which point there will still at least 65% of workers still in the warehouse. This is because the automation augments […]
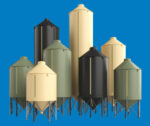
Silostore offers first-to-market composite silos
Silostore, Australia’s leading designer, manufacturer, and supplier of Glass Reinforced Plastic (GRP) composite silos, has revolutionised silo production by using a first-to-market, composite design. Silostore composite silos make handling of dry goods and liquids a far better experience for the end-user when compared to traditional materials such as concrete, aluminium, and steel for many reasons. “We have designed a world-class composite silo that gives the Australian market a more sustainable and far superior solution,” said Jerry Pridham, Director of Silostore. “The fact that we have been able to design and then manufacture such a revolutionary product right here in New South Wales is a phenomenal outcome for our industry.” The silos are fully sealed, have a very high insulation value, and do not rust. In addition, they are light-weight, easy to install, and virtually maintenance free. Externally, they are 100% UV-resistant, while internally they have a glass-like finish that ensures no internal catch points and excellent outflow properties. Zero condensation is also a bonus for grain storage and it also helps keeps the inside walls clean and reduces the risk of lump formation. Silostore silos include a market-leading 25-year warranty, never seen before in the industry. Silostore silos are ideal for the agriculture and food manufacturing sectors, as well as businesses such as seed and grain merchants, commercial bakeries and flour mills, pulp and paper, renewable energy, pet foods and liquid fertilizer industries. The superior weight-to-strength ratios and flexible design properties make them suitable for virtually any storage application across these sectors. With unforeseen events such as the Covid-19 pandemic, businesses are rethinking their global supply chains and looking for in-country solutions. As Australia’s only supplier of premium composite silos — backed by a proud century-long history as a leading manufacturer and supplier — Silostore can help combat the threat […]
Lead-free brass cable glands pioneer sustainability compliance trends
A new range of lead-free brass cable glands is being introduced by LAPP to help ensure manufacturers, machine builders and production automation engineers and operators achieve compliance with current and forthcoming global sustainability requirements. This will be the first manufacturer in the world to offer cable glands in a lead-free brass version, staying ahead of increasing restrictions on lead use. Initially, the most popular LAPP cable glands will be available in the new lead-free version, with first products including the popular Skintop MS-M and MS-SC-M models, as well as the counter nut Skindicht SM-M Skintop MS-M, which is the first choice for a wide range of applications in machine and plant construction, measurement, control and regulation technology, and where there are tough demands in terms of mechanical and chemical stability. It offers optimum strain relief, wide clamping ranges, numerous approvals and a high protection class from the full local branch of LAPP, which offers 20,000 products online 24/7 from local and global inventories of product and engineered solutions backed by outstanding local service and technical backing. LAPP says the Skintop MS-SC-M EMC cable gland, with highly conductive, flexible EMC contact spring, has a low-resistance screen contact for EMC-compliant earthing of the braided shield. All of these versions will be available immediately from stock in metric sizes M12 to M63. Further product groups are gradually being supplemented with lead-free versions. The previous versions will be still be available from global stock for the time being. In recent months, LAPP has investigated various lead-free alloys. This included tests in production to ensure the reliability of the processes and the suitability of the tools.